warrenpenalver
Active member
Bit of an update.
Wanted to replace my ancient sierra engine management loom for a while now so decided to get on with designing my loom. After some advice on here i have a loom design ive settled on.
This is the basic wiring diagram:
[/QUOTE]
I also measured a loom up and had to design my loom plan and adjust all the distances and branch lengths for my car. here is the sketch!
Purchased all the connectors, wiring etc and then made a start on the loom. Done everything that goes in or near the ECU plug. In essence ive done the easy bit
Then carried on down the loom adding the braid and heat shrink as i come to each break out.
I definitely prefer the kevlar braiding to the plastic braiding. More flexible and seems to be stronger gripped at the ends when its secured.
With all the braiding now at the end of the main loom, I started back at the beginning now on all the breakouts.
Completed my first breakout:
its nice to finally start putting on connectors meaning bits of the loom look actually finished.
both ignition amps done now. coil/coilpack wire done too with the third wire for coilpack hidden under heatshrink so when i convert i just take off the coil connectors, crimp on the coilpack terminals and connector and job done.
Also done the MAP connector as its big enough for the heat shrink ive got while i wait for the smaller stuff.
also got some terminals ive been waiting for. The terminals were from a BMW but fit the ford diagnostic plug connector housing i had spare, so now i have the proper connector on my new loom.
Also got the right connectors for the ford 3 pin LAMBDA connector. Couldnt find new connector housings anywhere so used new terminals and seals in a good secondhand housing. Got a white one to be different to boring black
and also have fitted a blanking end cap as i dont have a lambda on the car yet but will do eventually.
Also done one of the injector housings. Used yellow like ive seen on other looms and also right angle boots (in red!) as i got them free and again not boring black
Done a bit more and it finally is beginning to look a bit like a loom now!
Getting neater as i go along and learning tricks to keep things tidy too so if i do a car loom or some small sublooms in the future they will be neater as well.
All done! :content:
Wont be fitted for a while yet as i need to make all the other engine bay sublooms as im going for a complete front end rewire when i fit the engine loom.
Also will do a set of testing on the complete wire. Each wire has been checked its going from right pin to right connector, and also resistance checked to make sure i have good connections. next i want to again test every single wire now its assembled including a continuity check with ALL nieghbouring wires to make sure ive not damaged it some place during assembly.
Wanted to replace my ancient sierra engine management loom for a while now so decided to get on with designing my loom. After some advice on here i have a loom design ive settled on.
This is the basic wiring diagram:
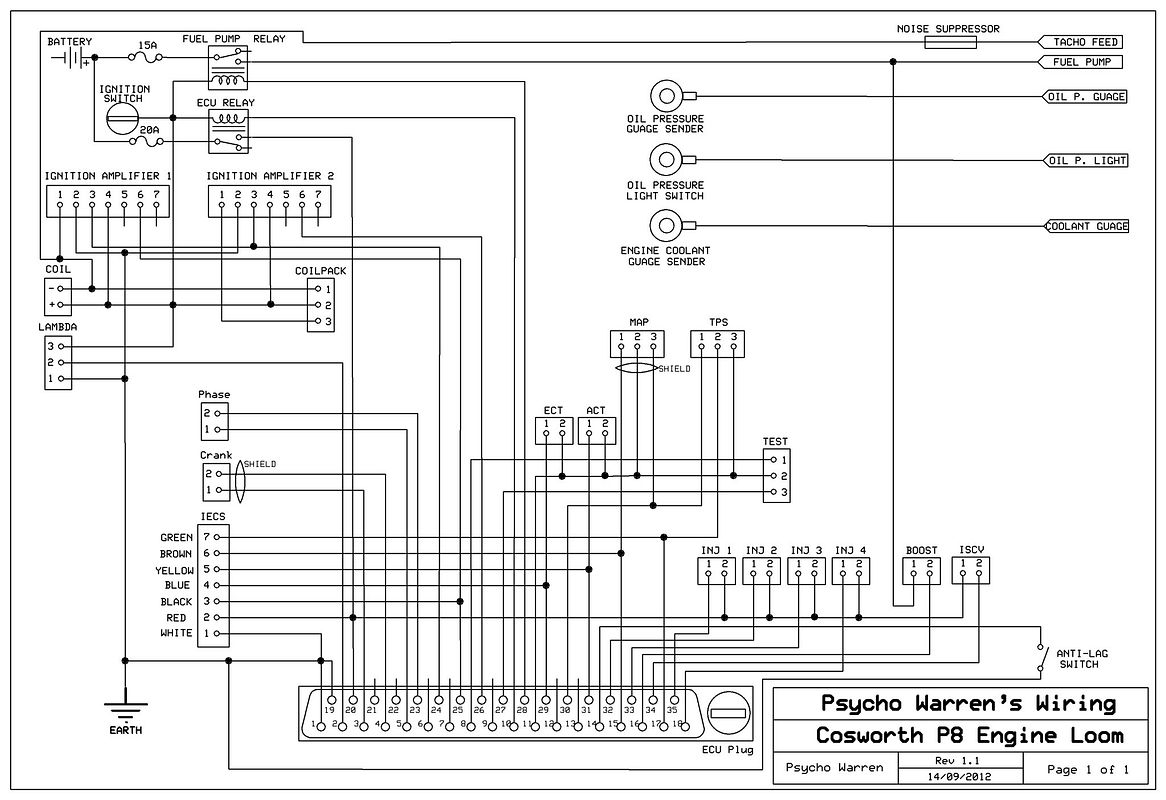
I also measured a loom up and had to design my loom plan and adjust all the distances and branch lengths for my car. here is the sketch!
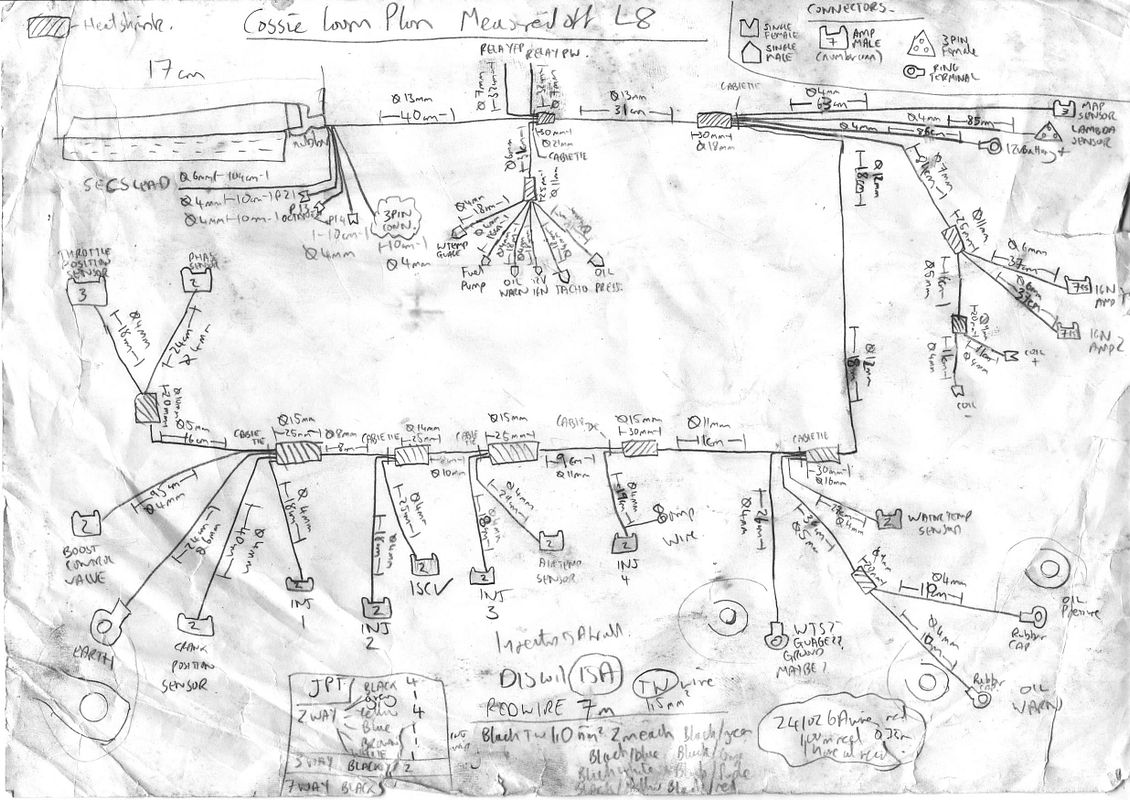
Purchased all the connectors, wiring etc and then made a start on the loom. Done everything that goes in or near the ECU plug. In essence ive done the easy bit

Then carried on down the loom adding the braid and heat shrink as i come to each break out.

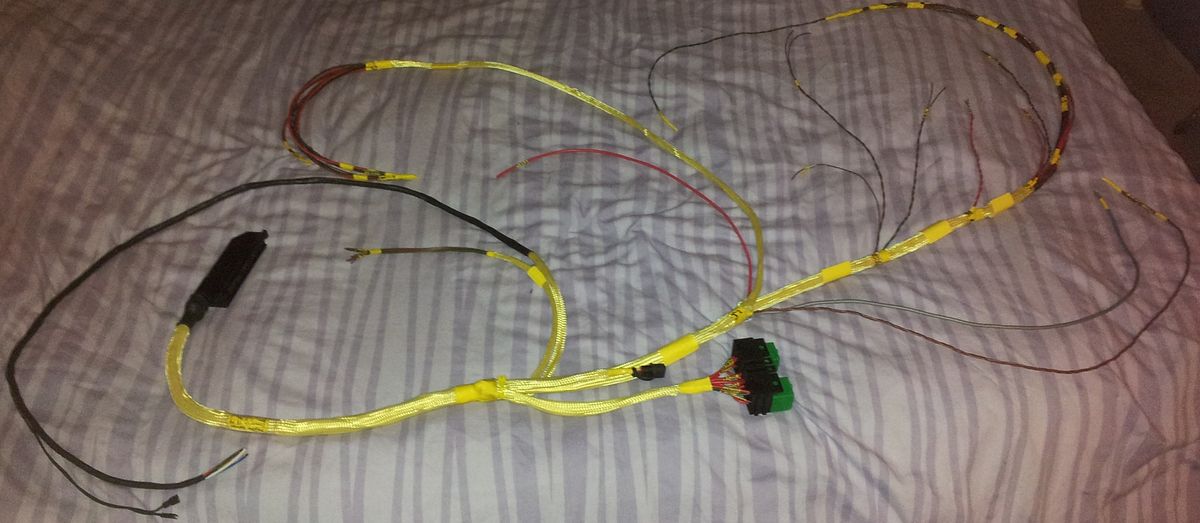
I definitely prefer the kevlar braiding to the plastic braiding. More flexible and seems to be stronger gripped at the ends when its secured.
With all the braiding now at the end of the main loom, I started back at the beginning now on all the breakouts.
Completed my first breakout:

its nice to finally start putting on connectors meaning bits of the loom look actually finished.
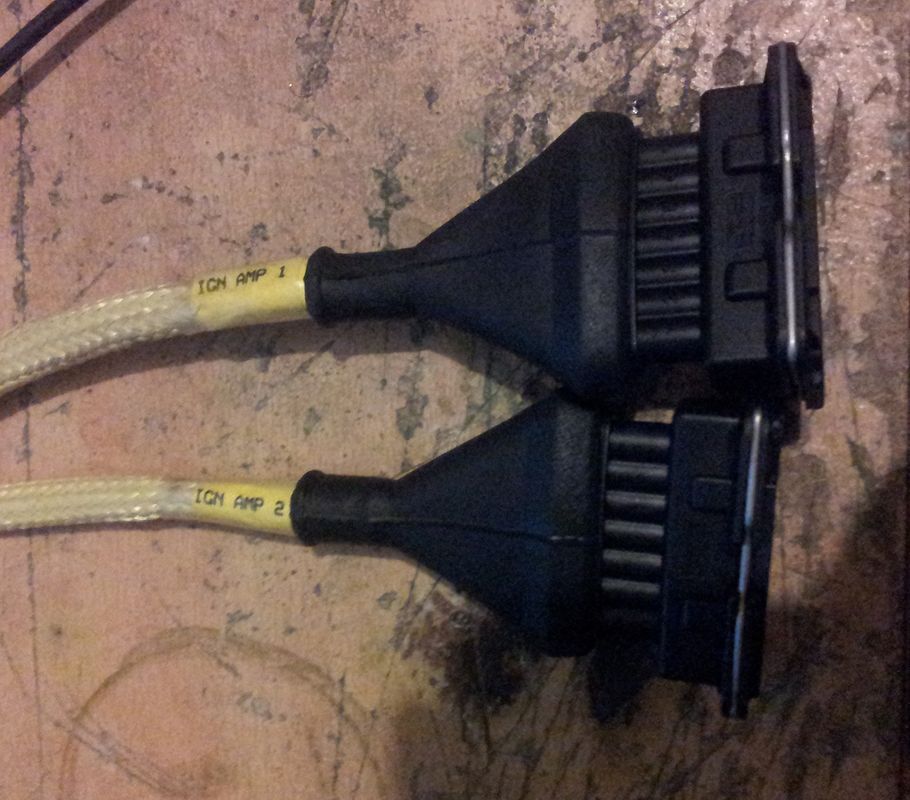
both ignition amps done now. coil/coilpack wire done too with the third wire for coilpack hidden under heatshrink so when i convert i just take off the coil connectors, crimp on the coilpack terminals and connector and job done.
Also done the MAP connector as its big enough for the heat shrink ive got while i wait for the smaller stuff.

also got some terminals ive been waiting for. The terminals were from a BMW but fit the ford diagnostic plug connector housing i had spare, so now i have the proper connector on my new loom.
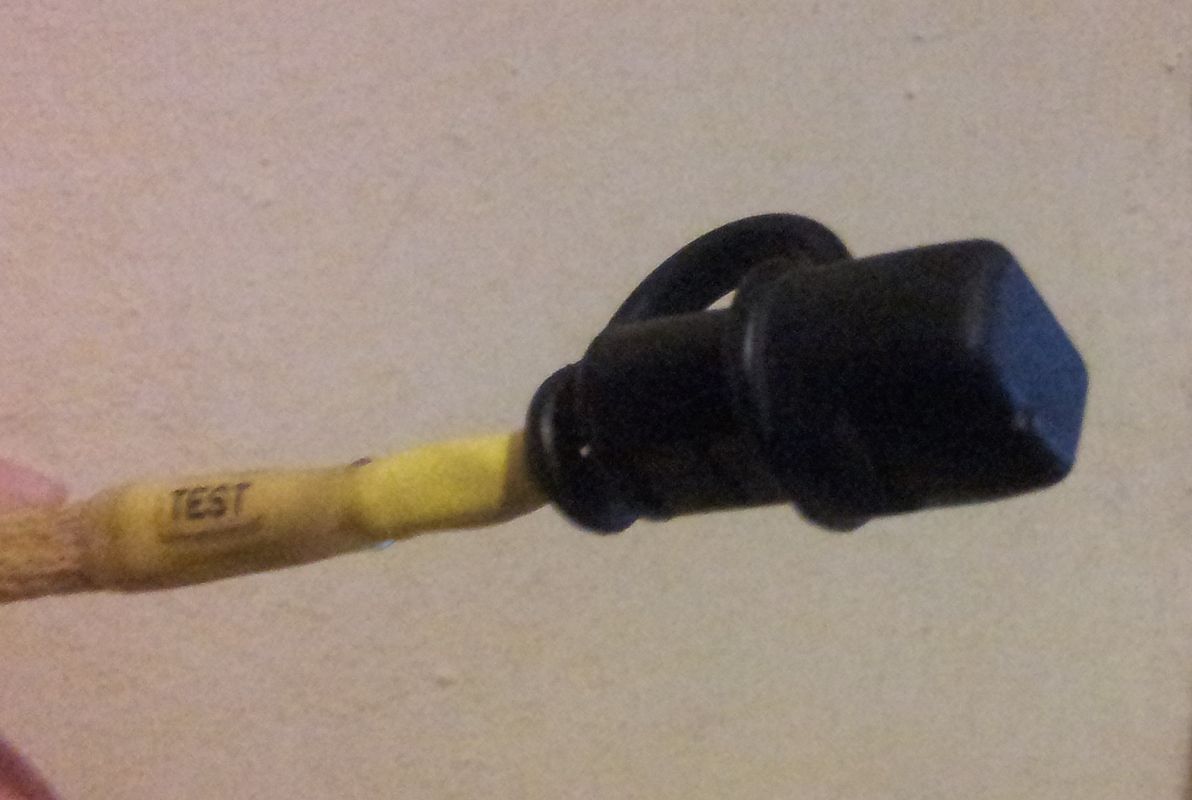
Also got the right connectors for the ford 3 pin LAMBDA connector. Couldnt find new connector housings anywhere so used new terminals and seals in a good secondhand housing. Got a white one to be different to boring black

Also done one of the injector housings. Used yellow like ive seen on other looms and also right angle boots (in red!) as i got them free and again not boring black
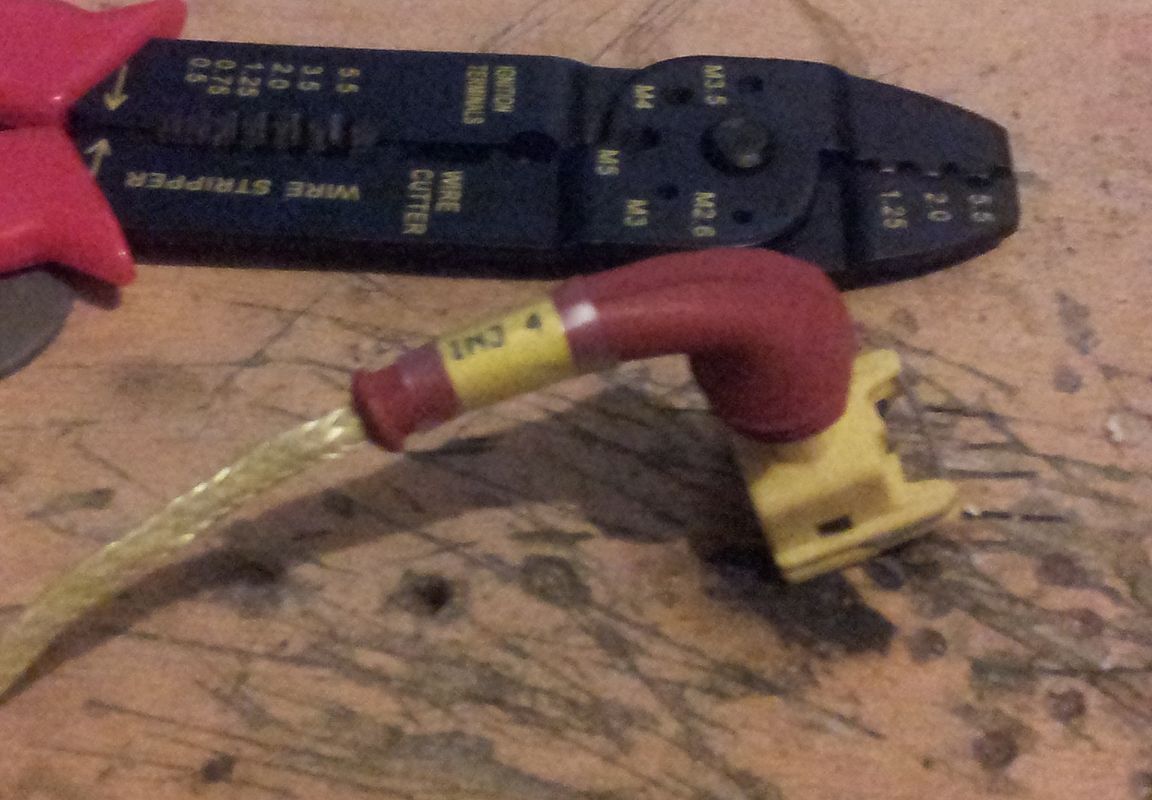
Done a bit more and it finally is beginning to look a bit like a loom now!

Getting neater as i go along and learning tricks to keep things tidy too so if i do a car loom or some small sublooms in the future they will be neater as well.
All done! :content:

Wont be fitted for a while yet as i need to make all the other engine bay sublooms as im going for a complete front end rewire when i fit the engine loom.
Also will do a set of testing on the complete wire. Each wire has been checked its going from right pin to right connector, and also resistance checked to make sure i have good connections. next i want to again test every single wire now its assembled including a continuity check with ALL nieghbouring wires to make sure ive not damaged it some place during assembly.